HDPE borular için kaynak masası. Isıtılmış bir aletle polietilen boruların kaynaklanması teknolojisi
Bir işçi HDPE boruya kaynak yapıyor
Makalenin içeriği:
Montaj kolaylığı nedeniyle 20 ila 1200 mm çapındaki HDPE borular sıklıkla kullanılmaktadır. Bu tüpler basınçlı veya basınçsız olabilir. Boruları bağlamak için (flanşlar ve bağlantı parçaları ile bağlantı) sökülebilir yöntemlerin yanı sıra, bir alın kaynak makinesi kullandığım polietilen boru ürünlerinin alın kaynağı ve polietilen boruların kaplinlerle bağlanması gibi tek parça yöntemler de vardır. Operasyonun gerçekleşeceği koşullara bağlı olarak belirli bir boru hattı bağlantısı türü kullanılır. HDPE boruların kaynaklanması en güvenilir yöntemdir.
HDPE boruların kaynağı: teknoloji ve uygulama.
Sistem basınç altında kalacaksa genellikle HDPE boruların kaynağını kendi elleriyle kullanırlar.
Polietilen boruların kaynağı kullanılacaktır çeşitli türler:
- alın kaynağı;
- elektrofüzyon kaynağı;
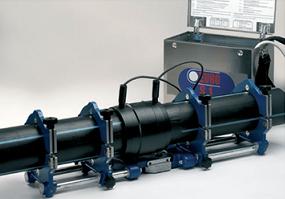
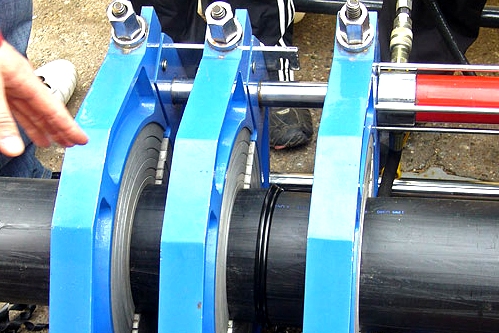
Gerçekleştirilmeden önce HDPE borularını kendi ellerinizle kaynaklamak, her şeyi hazırlamanız gerekiyor:
- Gelecekteki HDPE alın kaynağı bağlantısının alanlarını mekanik olarak işleyin;
- HDPE boruların kaynaklanması için ekipman kontrol edilir. Burada daha ayrıntılı olarak duracağız;
- cihazı servis kolaylığı açısından görsel olarak kontrol etmelisiniz;
- elektrik jeneratörüne yakıt ikmali yapın ve deneme çalıştırması yapın;
- kazıyıcı, düzeltici ve diğer bileşenler yapışan polietilenden temizlenmelidir;
- Hidrolik sistemdeki yağ miktarını kontrol edin.
HDPE alın kaynağı
HDPE boruların kaynaklanması Kendin yap popo birleştirme işlemi elektrofüzyondan daha zordur. Yeteneklerinize güveniyorsanız, kaynak yeterliliği ve deneyimine sahipseniz süreci üstlenin. Kaynağın az enerji tüketen ekonomik bir işlem olduğunu unutmayın.
HDPE alın kaynak makinesi, kalite ve özellik bakımından ana malzemeye eşit yekpare bir dikiş oluşturur. Polietilen borular, bağlantı parçaları vb. bu şekilde bağlanır. Bu yöntem sadece aynı marka ve çaplarda, et kalınlığı 4,5 mm'yi, çapı 50 mm'yi geçmeyenler için geçerlidir. Sıcaklık HDPE boru hattının kaynaklanması da önemlidir, bağlantı -14C ila +47C sıcaklık aralığında yapılmalıdır.
HDPE borular için ortalama kaynak sıcaklığı 130-140 derecedir.
Yöntem özel varlığı gerektirir teçhizat.
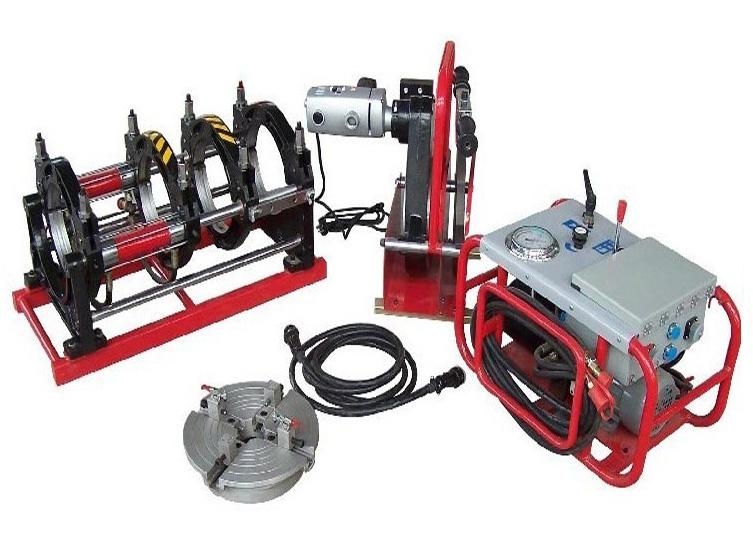
- Vernier kumpaslar - malzemenin boyutlarını ölçmek için;
- Merkezleyici – boruların eksenel yönde sıkıştırılmasını sabitlemek için;\
- Düzeltici - mekanik işleme için;
- Hidrolik tahrik – hassas ayar ile borular üzerinde sabit basınç için.
Alın kaynağı polietilen tel: prosedür ve eylem planı
- polietilen ürünün ovalliğini, boyutların uyup uymadığını kontrol edin ve elektrikli bir düzeltici ile olası düzensizlikleri giderin;
- boruları, uçlar arasında 4 cm'lik bir mesafeyi koruyarak merkezleyiciye takın;
- Bunu kaynak aparatı ile uçların eritilmesi takip eder ve eritme işlemi başlar;
- HDPE boru hattı için kaynak tablosunun seçim yapmanıza yardımcı olacağı şekilde borunun belirli bir süre ısıtılması gerekir.
- Isıtmanın hemen ardından HDPE, boruların ısıtılmış uçları kullanılarak uçtan uca bağlanır.
- Daha sonra boru alın kaynak makinesi gerekli basıncı üretir ve ardından son çapak oluşturulur.
Polietilen soğuduktan sonra yaka sızdırmaz bir dikiş oluşturulur. Boru duvarının kalınlığının %9-10'undan fazla bozulmasına izin verilmemelidir.
Polietilen boru kaynak tabloları
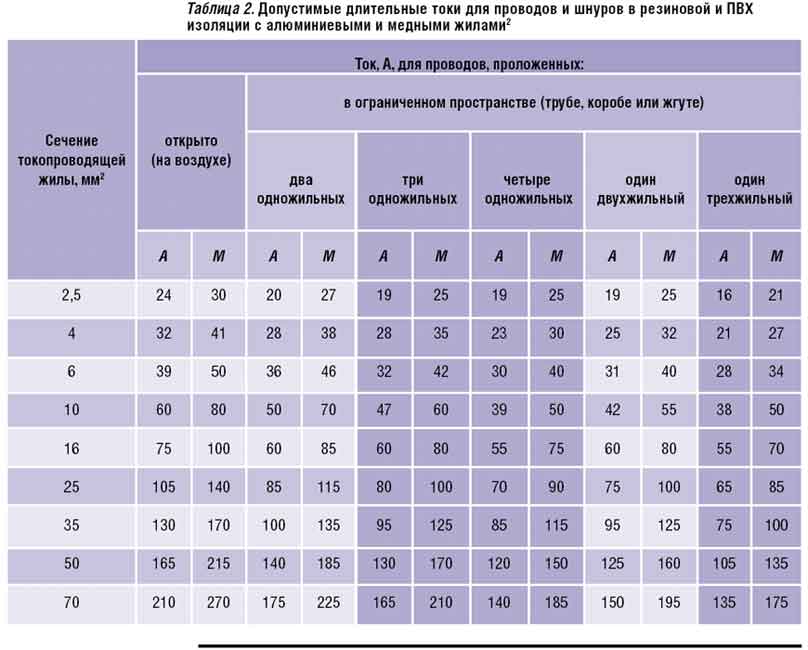
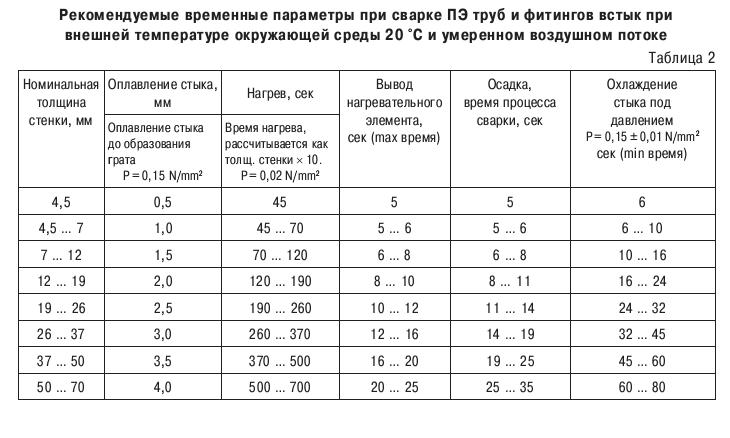
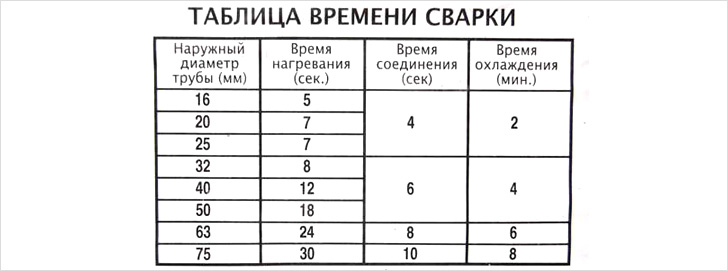
Polietilen boruların video kaynağı
Polietilen boruların kaplinlerle kaynağı
Bu yöntem ekonomik açıdan daha az karlıdır ancak küçük alanlarda uygundur. Elektrofüzyon Polietilen boruların kaynağı genellikle onarımlar sırasında kullanılır, bu, çapı 150-160 mm'ye kadar olan teller için çok önemlidir. Ek bir manşon oluşturmanız gerekiyorsa bu yöntem de uygun olacaktır. Düzgün oluşturulmuş bir bağlantı 14-16 atmosfer basınca dayanacaktır.
HDPE kaplinlerin kaynaklanması
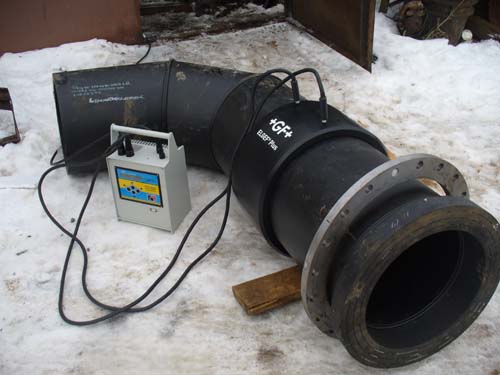
Elektrik bağlantısı HDPE malzemeden yapılmış, içerisinde elektrik spiralleri bulunan çeşitli boyutlarda şekillendirilmiş bir parçadır. Farklı bağlantı türleri için farklı formlar vardır.
Kaynak dikişi oluşturmak:
- boruların yağ ve diğer istenmeyen maddelerden kirlenmesinin giderilmesi;
- kaplin spiraline verilir elektrik bu da etilenin sıcaklığını arttırır ve onu eritir.
- daha sonra alttaki uçlar ısıtılır. kaplin
- boru hattı genişler, böylece kaynak için gerekli basınç oluşturulur.
- elektrik kapatılır ve kaynak yapılan HDPE boru soğur, böylece güvenilir, hava geçirmez bir bağlantı oluşturulur. Soğuduktan sonra çıkarılır ve bir belge yazdırılır - bir elektrikli kaynak protokolü.
HDPE boruların video-elektrofüzyon kaynağı.
Video talimatı
HDPE kaynağı: fiyat, kira
Birçok şirket de büyük şehirler HDPE boruların kaynaklanması için bir makine kiralama hizmeti sunuyoruz. Kullanıcı, bir kaynak makinesi satın alma ve geçici kullanım için alma ihtiyacını ortadan kaldırarak para tasarrufu sağlar.
Avantajları kiralama kaynak makinesi.
- uzman. ekipman oldukça pahalıdır, kiralamak tasarruf etmenizi sağlar;
- Değişen ihtiyaçlarınıza uygun geniş bir ekipman yelpazesi mevcuttur.
Fiyat kira günlük 2 ila 4 bin ruble arasında değişiyor.
Kaynaklı bağlantılar kalıcıdır; parçaları kırılmadan sökülemez. Bu, kaynaklı bağlantıların sağlamlığını (sürekliliğini) gösterir. Böyle bir yekparelik, bağlanan parçaların yüzey makromolekülleri arasında etkileşim kuvvetleri (van der Waals kuvvetleri) ortaya çıkarsa ve bunların bir parçadan diğerine karşılıklı hareketi, örneğin difüzyon nedeniyle meydana gelirse sağlanabilir.
Kaynak yapılan plastiğin yüzey makromolekülleri arasında bağların oluşması, arayüzün kaybolması ve kaynak yapılması için bu kuvvetlerin gözle görülür şekilde kendini göstermeye başladığı mesafelerde (0,3-0,4 nm) yüzeyleri bir araya getirmek yeterli gibi görünmektedir. meydana gelmek. Kaynaklamayı, polimer makromoleküllerin karşılıklı difüzyonuna ve kimyasal etkileşimine dayanan, bunun sonucunda bağlı yüzeyler arasındaki arayüzün oluştuğu, bir ürünün parçalarının kalıcı bir bağlantısını elde etmek için teknolojik bir süreç olarak tanımlayan bazı yazarlara rehberlik eden bu düşüncelerdir. kaybolur.
Ancak ideal durumda bile, birleştirilen yüzeyler mikro pürüzlülüklerden (ideal olarak pürüzsüz yüzeyler), çeşitli kirletici maddelerden, adsorbe edilmiş gazlardan ve bu yakınlaşmayı engelleyen diğer bileşenlerden arındırıldığında, dışarıdan deformasyon ve termal enerji harcamak gerekir. Deformasyon enerjisi, yaklaşan yüzey atomları arasında ortaya çıkan itici kuvvetlerin üstesinden gelmek için harcanacaktır. Termal enerji aralarındaki etkileşim olasılığını artırır. Bu tür fikirlerden hareket edersek, kaynak bölgesinde iki ana süreç ayırt edilebilir: Birincisi enerjinin temini ve dönüşümü, ikincisi ise maddenin hareketi (veya dönüşümü). Enerji dönüşüm sürecinin yoğunluğu ve doğası kaynak türünü belirler.
Kaynak işleminin gerçekleştirilmesi için kaynak yapılacak yüzeylerin aktivasyonu gereklidir. Bu, enerji tedarik edilerek ve bazı durumlarda dönüştürülerek elde edilir. Maddenin eklenmesi yalnızca belirli plastik kaynak türleri için gereklidir, örneğin dolgu malzemesi kullanılarak ısıtılmış gazla kaynak yapılırken ve ayrıca eriyik ile kaynak yapılırken. İkinci durumda enerji dolgu malzemesi ve eriyik ile sağlanır.
Çeşitli plastik kaynak türleri sırasında malzemenin hareketi önemli olabilir. Viskoz akış durumuna kadar ısıtılan malzemede meydana gelen karıştırma ve difüzyondan kaynaklanır. Özel bir hareket türü, kaynak yapılan yüzeylerde bulunan aktif grupların birbirleriyle veya bir ara maddenin aktif gruplarıyla kimyasal reaksiyonu olarak düşünülmelidir; bu, aynı zamanda bir tür enerji sağlandığında da meydana gelebilir (kimyasal kaynak) .
Yukarıdakilere dayanarak, plastik ve metallerin kaynağının tanımında termodinamik anlamda hiçbir fark olamayacağını varsayabiliriz. Bu tanım şu şekilde formüle edilebilir: kaynak, bağlantı noktasında enerji ve maddenin girişi ve termodinamik olarak geri dönüşü olmayan dönüşümü nedeniyle malzemelerin monolitik bir bağlantısını elde etme işlemidir.
Kaynak işleminin mekanizması ve plastiklerin kaynaklanabilirliği
Modern kavramlara göre kaynak işlemi topokimyasal bir reaksiyon olarak değerlendirilmelidir; bir katının yüzeyinde meydana gelen kimyasal reaksiyon. Herhangi bir kimyasal reaksiyonun temeli, orijinal maddelerdeki bağların kırılması ve yeni bağların oluşması ve bunun sonucunda yeni bir maddenin oluşması sürecidir. Bu nedenle bir kaynak yönteminden diğerine ve bir malzemeden diğerine geçerken bağlantı oluşum mekanizması değişmemelidir. Yalnızca temas yüzeylerindeki olayların bütünlüğü değişir ve onları bir etkileşim durumuna getirir. Bu olaylar farklı olabilir ve malzemenin doğasına ve kaynak yöntemine göre belirlenir.
Bir topokimyasal reaksiyon üç aşamayla karakterize edilir: fiziksel temasın oluşması; temas yüzeylerinin aktivasyonu; etkileşimin hacimsel gelişimi.
Fiziksel temasın oluşumu genellikle kaynak yapılan parçalara basınç uygulandığında meydana gelir. Bazı durumlarda, erimiş dolgu malzemesi kaynak bölgesine girdiğinde, bununla kaynaklı kenarlar arasındaki fiziksel temas, basınç uygulanmadan veya nispeten düşük bir basınçta gerçekleştirilebilir. Bu, sıcak gaz kaynağı ve ekstrüzyon kaynağı için geçerlidir.
Kaynak yapılacak yüzeyler arasında fiziksel temasın kurulması ısıtmadan önce yapılabilir, birleştirilecek yüzeylerin kaynak sıcaklıklarına ısıtılmasından sonra veya ısıtmayla eş zamanlı olarak gerçekleştirilebilir. Her durumda, bu aşamada, temas eden yüzeylerin birbirine yaklaşması nedeniyle makro ve mikro düzensizliklerin plastik deformasyonu meydana gelir. Deformasyon işi ayrıca yabancı kalıntıların (gaz kabarcıkları, yağ ve gres lekeleri ve diğer kirletici maddeler) temas bölgesinden uzaklaştırılması için de harcanır. Yumuşak plastikler ve lifli malzemeler için bu aşamada sıkıştırma karakteristiktir ve malzemenin kalınlığında bir azalma ile kendini gösterir.
Kaynak yapılacak yüzeylerin aktivasyonu, makromoleküllerin termal hareket enerjisini arttırmak için bunların ısıtılmasını içerir. Isıtma, ısıtılan aletten, gazdan veya dolgu malzemesinden ısının doğrudan kaynak yapılan parçalara aktarılmasıyla veya diğer enerji türlerinin termal enerjiye dönüştürülmesiyle gerçekleştirilebilir. Bu, ultrasonik titreşimlerin veya sürtünmenin mekanik enerjisi, bir kapasitörün yüksek frekanslı elektrik alanının enerjisi, elektromanyetik enerji, kızılötesi radyasyonun enerjisi, bir lazer ve konsantre bir ışık huzmesi olabilir.
Çeşitli enerji türlerinin yüzeylerin termal termal aktivasyonuna dönüştürülmesini kullanarak kaynak yaparken, bu tür kaynağın özellikleriyle ilgili işlemlerden önce gelecektir: dipollerin yer değiştirmesi - yüksek frekanslı akımlarla kaynak yaparken.
Ultrasonik kaynak sırasında ultrasonik titreşimlerin girişi ve yayılması, ayrıca mekanik titreşimlerin enerjisinin konsantrasyonu ve termal enerjiye dönüştürülmesi; radyasyon enerjisinin emilimi - kızılötesi radyasyonla kaynak yaparken.
Statik ve ultrasonik kaynakta dinamik yüklerin etkisi, aletin onunla temas eden parçanın yüzeyine nüfuz etmesine yol açtığından, termal aktivasyon aşamasına deformasyon süreçlerinin gelişimi de eşlik edebilir. plastikleşmiş veya erimiş malzemenin kaynak bölgesinden yer değiştirmesine.
Etkileşimin hacimsel gelişimine, aralarında en önemlileri difüzyon, akış ve fizikokimyasal dönüşümler olan bir dizi karmaşık fizikokimyasal süreç eşlik eder. Bu aşamada baskın rolün difüzyona verildiği kaynak teorisine difüzyon denir. Kaynaklanabilirlikten akış süreçlerinin sorumlu olduğuna inanılan teoriye, akış yasalarını inceleyen reoloji biliminin adından sonra reolojik denir.
Difüzyon teorisine göre bir bağlantının sağlanabilmesi için, bir maddenin iki yüzeyi temas ettiğinde yeterince tam bir füzyonun (kaynaşma) meydana gelmesi gerekir. İki sıvı tabakasının tamamen birleşmesi doğrudan temas halinde meydana gelir ve buna aralarındaki arayüzün kaybolması eşlik eder. Polimerlerin birleştirilmesi durumunda, birleşme için tek bir temas yeterli değildir, çünkü makromoleküllerin bir bütün olarak veya tek tek bölümler halinde difüzyonu yoluyla elde edilebilecek olan temas bölgesinde yapı oluşumunun yine de meydana gelmesi gerekir. Segmentlerin hareketi, makromolekülün geri kalanıyla bağlantıları nedeniyle engellenir, dolayısıyla segmentlerin difüzyonu, zincir molekülünün konfigürasyonunda bir miktar değişikliğe neden olur. Bunun bir sonucu olarak, segmentlerin birbirini izleyen çok sayıda hareketi, yalnızca makromoleküllerin şeklinde bir değişikliğe değil, aynı zamanda ağırlık merkezlerinin de yer değiştirmesine yol açacaktır. Segmentlerin ve makromoleküllerin bir bütün olarak hareketine sırasıyla mikro-Brownian ve makro-Brownian hareketi denir.
Tüm makromoleküllerin hareketi, polimer katmanlarının teması akış sıcaklığının üzerindeki bir sıcaklıkta meydana gelirse özellikle kolaylıkla gerçekleşebilir. Bu durumda bir polimerin yapı özelliği temas bölgesinde nispeten kolay bir şekilde ortaya çıkar. Molekülün bir bütün olarak hareketi zorken, makromoleküllerin tek tek bölümlerinin difüzyonu, polimerin oldukça elastik durumuna karşılık gelen sıcaklıklarda da meydana gelebilir. Bu tür sıcaklıklarda birleşme derecesi birlikten daha azdır (maksimum birleşme derecesi birliğe eşittir ve yalnızca sıvılarda gözlenir), bu da bölümlerin belirli bir derinliğe hareket etmesinden sonra difüzyonun durmasıyla açıklanır. Moleküler zincirlerde ortaya çıkan stresler.
Kaynak işleminin difüzyon doğasının kanıtı, termal hareketi teşvik eden tüm önlemlerin (basınç ve sıcaklığın arttırılması, plastikleştiricilerin eklenmesi vb.) kaynaklı bağlantının mukavemetinde bir artışa neden olması ve bunun tersine, difüzyonu yavaşlatan faktörler olabilir. gücü azaltın.
Reolojik teorinin savunucuları, bağlantının oluşumundan yalnızca difüzyon sorumlu olsaydı, kaynak süresinin onlarca dakika olacağını belirtiyorlar. Ancak pratikte bu süre çok daha azdır. Ayrıca, hava boşlukları ve kaynak yapılan malzemelerin yüzey katmanlarının kirlenmesi nedeniyle difüzyon işleminin kaçınılmaz olarak engellendiği, dolayısıyla nüfuz etme süresinin daha da arttığı dikkate alınmalıdır. Son olarak, makromoleküllerin bölümleri arayüze nüfuz ettikçe inhibisyonlarının sürekli olarak artması nedeniyle difüzyon katsayısının sabit kalmadığı, sürekli azaldığı akılda tutulmalıdır.
Bu nedenle, reolojik teorinin destekçileri, moleküller arası etkileşim ve temas halindeki hacimlerdeki difüzyon kuvvetlerinin tezahüründen önce, eriyiğin akışı ve karışımıyla ilişkili bir dizi olayın gerçekleştiğini varsayarlar (1-4, 16|.
Erimiş yüzeyler temas ettiğinde, kenetleme kuvvetinin yarattığı gerilimlerin (ve ultrasonik kaynakta dinamik gerilimlerin) eriyik katmanlarında bir kaymaya neden olduğuna inanılmaktadır. Böyle bir kaydırma ile bağlantı bölgesinden hava boşluğu ve diğer yabancı kalıntılar uzaklaştırılır ve eriyik kaynak bölgesinden dışarı sıkılır, bu da yüksek kalitede kaynaklı bir bağlantının elde edildiğini gösterir. Temas eden yüzeylerin farklı alanlarındaki kayma hızı, sıcaklıkların ve gerilimlerin eşit olmayan dağılımı nedeniyle değişebilir. Bütün bunlar eriyiğin temas eden hacimlerde karışmasına neden olabilir; bu özellikle yüksek frekanslı mekanik (ultrasonik kaynak) veya elektriksel (Yüksek Frekanslı kaynak) titreşimler |1-4 kullanılarak yapılan kaynak durumlarında olasıdır.
Kaynak bölgesinde viskoz akan malzemenin karıştırılması olgusu, plastiklerin ısıtılmış bir aletle kaynaklanması işlemi incelenirken deneysel olarak doğrulandı. Görünüşe göre kaynak sırasında viskoz akan malzemenin makro hacimleri bir karıştırma işlemiyle, mikro hacimleri ise bir difüzyon işlemiyle karakterize edilir.
Kaynak oldukça elastik sıcaklık aralığında gerçekleştiriliyorsa difüzyon mekanizması baskındır. Bu durumda, kaynaklı yüzeylerin birbirleriyle uzun süreli teması gereklidir, kaynaklar arayüzü korur ve bağlantı bölgesindeki malzeme, supramoleküler yapı bakımından orijinalinden farklı değildir. Bu tür kaynaklama önemli basınçlarda meydana gelir ve bu da bağlantının soğumasından sonra kaynak bölgesinde önemli artık gerilimlere neden olur [7-10].
Kaynak, viskoz akış sıcaklığı aralığında (amorf polimerler için) veya erime sıcaklığı aralığında (kısmen kristalli polimerler için) gerçekleştirilirse, işlem metal kaynağına benzer. Dış kuvvetlerin etkisi altında, katmanların hareketi ve karışmasıyla birlikte eriyiğin hızlı birleşmesi meydana gelir. Bu durumda, gaz ve oksit kalıntıları içeren eriyik katmanları kaynak bölgesinden çıkarılır, bu da moleküler zincir bölümlerinin ve tüm makromoleküllerin mikro hacimlerde karşılıklı difüzyonunu kolaylaştırır. Bu tür bağlantıların kaynaklarında, bağlanan yüzeyler arasında pratik olarak hiçbir arayüz yoktur. Orijinal temas düzlemi boyunca çökmezler ve supramoleküler yapı, eriyiğin soğuma koşullarına bağlı olarak değişebilir (19-11).
Son aşamada ergitme kaynağının eriyik akışıyla ilişkili olması nedeniyle, plastiklerin kaynaklanabilirliği, viskoz akışın aktivasyon enerjisi, viskoz akış durumunun sıcaklık aralığı ve viskozite gibi özelliklerle değerlendirilir. erimenin. Bu fikirlerin ışığında, viskoz akışın aktivasyon enerjisi ve eriyiğin viskozitesi ne kadar düşükse ve viskozite-akışın sıcaklık aralığı ne kadar genişse, yüksek kaliteli kaynaklı bir bağlantının oluşma ihtimalinin o kadar yüksek olduğu açıkça ortaya çıkıyor. Reolojik özelliklerine göre plastikler üç gruba ayrılabilir (1, 4, 10, 16, 18, 19|.
Birinci grup, viskoz akışın aktivasyon enerjisinin kimyasal bağ enerjisinden önemli ölçüde düşük olduğu ve 150 kJ/mol'ü aşmadığı yönlendirilmemiş termoplastikleri içerir; viskoz akış durumunun sıcaklık aralığı (Tt ve Tr, burada Tt akışkanlık sıcaklığıdır ve Tr ayrışma sıcaklığıdır) 50 °C'yi aşar; erime viskozitesi 102-105 Pa'dır. İle.
Bu tür termoplastikler ısıtıldığında, termal tahribat olmaksızın viskoz akış durumuna dönüşür ve oldukça geniş bir sıcaklık aralığında viskoz akış durumunda kalır; bu durumda eriyiğin viskozitesi, az bir çabayla hızlı ve tam birleşmenin sağlanabileceği şekildedir. Bu termoplastikler, çok çeşitli koşullarda çeşitli kaynak yöntemleri kullanılarak füzyonla iyi bir şekilde kaynaklanır. Bu termoplastik grubunun en tipik temsilcileri poliolefinlerdir.
İkinci grup yukarıda belirtilen reolojik özelliklere sahip yönlendirilmiş termoplastikleri içerir; viskoz akışın yüksek aktivasyon enerjisine sahip (kimyasal bağlanma enerjisine yakın) yönlendirilmemiş ve yönlendirilmiş termoplastikler; akışkanlık sıcaklığı ile ayrışma sıcaklığı arasında dar bir aralığa (50 ° C'den az) ve nispeten yüksek erime viskozitesine sahip termoplastikler.
Viskoz akışın yüksek aktivasyon enerjisine sahip termoplastikler için, viskoz yığın durumuna ısıtıldığında tahrip olma tehlikesi vardır. Tt ile Tp arasında dar bir sıcaklık aralığına sahip olan termoplastikler hafif aşırı ısınmayla ayrışabilmektedir. Yönlendirilmiş termoplastiklerde, viskoz-akışkan duruma ısıtıldığında malzemenin mukavemetini sağlayan yönlendirilmiş yapı kaçınılmaz olarak bozulur. Yüksek erime viskozitesine sahip termoplastikler için, eriyiğin tamamen kaynaşmasını ve karışmasını sağlamak zordur.
Bu tür termoplastiklere yalnızca belirli zorunlu koşullar altında ergitme kaynağı yapılabilir. Yönlendirilmiş malzemeler ve Tt ile Tp arasında dar bir aralığa sahip malzemeler için, ergitme kaynağı, malzemenin yanlış yönlendirilmesine ve tahribatına neden olmamalıdır; bu, yalnızca kaynak yapılan yüzeylerin akışkanlık sıcaklığına nüfuz etmeden hızlı ve lokal ısıtma koşuluyla mümkündür. Malzemenin tüm kalınlığı boyunca. Eriyik viskozitesi 105 Pa'nın üzerinde olan termoplastiklere gelince. s, daha sonra ergitme kaynakları ancak kaynak işlemi sırasında eriyiğin viskozitesinin azaltılması durumunda mümkündür. Sonuç olarak, bu gruba ait termoplastiklerin ergitme kaynağı olasılığını sağlamak için, her özel durumda en uygun kaynak yöntem ve tekniklerini bulmak gerekir.
Bu grup, polivinil klorür, poliviniliden klorür, pentaplast, polietilen tereftalat, polikarbonat, eriyebilir floroplastikler ve diğer termoplastikleri içerir.
Üçüncü grup, viskoz akış aktivasyon enerjisi kimyasal bağ enerjisini aşan termoplastiklerin yanı sıra erime viskozitesi 1011 - 1012 Pa olan termoplastikleri içerir. İle. Bu termoplastikler viskoz akış durumuna dönüştürülemez; ergitme kaynağı yapılamaz. Bunlar arasında örneğin floroplastik-4, selüloz asetat, polivinil asetat yer alır. Bu tür termoplastiklerin bağlantılarının oluşumu, yalnızca yüzeylerin oldukça elastik bir durumun sıcaklıklarına kadar ısıtılmasıyla difüzyon kaynağı mekanizması ile mümkündür; mümkün olan en yüksek seviyede, kaynak yapılan malzemelerin zorlanmış esneklik sınırına eşit basınç altında uzun süre maruz kalma sıcaklık.
Difüzyon kaynağının hızlandırılması, bu termoplastiğin şişip çözülebildiği solventler kullanılarak sağlanabilir. Solventler makromoleküllerin hareketliliğini arttırır, böylece kaynak sıcaklığı azaltılabilir.
BORU HATLARININ MONTAJI SIRASINDA PE BORULARIN DİREK ISITMA İLE KAYNAĞI
Polietilen boruların alın kaynağı
Plastik boru hatları son yıllarda hem ülkemizde hem de yurt dışında yaygın olarak kullanılmaktadır. Plastik boru hatlarının bu kadar yaygın kullanımı, çelik borulara göre 4-5 kat daha hafif olmaları, agresif ortamlara karşı yüksek direnç göstermeleri ve hidrolik direncinin daha düşük olmasından kaynaklanmaktadır. Plastikten yapılmış boru hatlarının kurulumu ve işletilmesi için işçilik maliyetleri, yüksek kaliteli karbon çeliklerinden yapılmış boru hatlarından ortalama 2 kat, paslanmaz çelikten yapılmış boru hatlarından ise 3-4 kat daha azdır.
En yaygın olarak kullanılanlar, çapı 315 mm'ye kadar olan düşük ve yüksek yoğunluklu polietilen, polipropilen ve polivinil klorürden yapılmış borulardır. Yakın gelecekte çapı 630 mm'ye kadar olan yüksek yoğunluklu polietilen boruların kullanılması planlanıyor. Boru hattı inşaatı sırasında bu tür boruların ana bağlantı türü alın kaynağıdır.
Tablo 4.1. Bazı termoplastiklerin ısıtmalı bir aletle kaynak modunun parametrelerinin yaklaşık değerleri (doğrudan ısıtma)
* Işık karbon siyahı ile stabilize edilmiştir.
Üretimin çeşitli aşamalarında bir dizi kontrol önlemi alınarak plastik boru hatlarının yüksek kaliteli kaynaklı bağlantıları sağlanır. Bu kompleks üç aşamadan oluşur: önleyici kontrol (kaynağa başlamadan önce), aktif (kaynak işlemi sırasında) ve kabul kontrolü (kaynağın tamamlanmasından sonra).
Önleyici kontrol, kaynaklı malzemelerin kalite kontrolünü, performans göstergeleri dikkate alınarak kaynak ekipmanının seçimini, kaynakçıların niteliklerinin kontrol edilmesini ve üretimin teknolojik hazırlığının kontrolünü içerir.
Depoya vardığınızda boruları, geometrik parametrelere benzer boruların montaj için alınmasını sağlayacak şekilde sıralamak gerekir. Yüzeylerinde ve uçlarında çıplak gözle görülebilen çatlaklar, kabarcıklar, boşluklar ve yabancı kalıntılar, soğuk bağlantı izleri ve malzemenin ayrışması olmamalıdır.
Boruların depolama koşulları, bunların doğrudan güneş ışığına maruz kalmasını önlemelidir; çünkü bu sadece boru malzemesinin mukavemetini azaltmakla kalmaz, aynı zamanda kaynaklanabilirliklerini de önemli ölçüde bozabilir.
Kaynak yapılmadan önce borular mekanik ve termo-mekanik testlere tabi tutulur.
Boruların garantili raf ömrü üretim tarihinden itibaren iki yıldır. Belirlenen süre sonunda borular kullanılmadan önce tekrar kontrol edilmelidir.
PE boruların kaynaklanması - kaynak ve montaj için hazırlık
Boruların montaj ve kaynak için hazırlanması büyük önem taşımaktadır. Uçtan en az 30 mm mesafede kaynak yapılan boruların uçlarının iç ve dış yüzeyleri, kaynaklanabilirliği olumsuz yönde etkileyen ve çalışma sırasında kaynağın çatlamasına neden olan toz, yağ, karbon siyahı ve diğer kirleticilerden arındırılır. Kaynak tesisatında kelepçelenen boruların birleşen yüzeyleri temizlendikten sonra traşlama işlemine tabi tutulur. Düzeltme sırasında oluşan talaşlar temiz bir bezle veya iş parçalarının uçlarının kirlenmesini önleyen başka bir yöntemle çıkarılır. Bazı durumlarda kaynaklı uçların bir solvent (aseton, alkol) ile yağdan arındırılması kullanılır. Deforme olmuş, yırtılmış veya çentikli boru uçları kesilir. Kenarları işlemeden önce kesici aletin yağdan arındırılması gerekir. Soğutma emülsiyonları ve yağlayıcıların kullanılması yasaktır.
Sonraki önemli işlemler kaynak öncesi boruların montajı ve hizalanmasıdır. Bu işlemler, kaynak yapılacak özel bir cihaz veya tesisat üzerinde yapılmalıdır. Birleştirilen boruların uçları, boru uzantısının 60-70 mm olması için kaynak tesisatının halka kelepçelerine (merkezleyiciler) sabitlenmesi gerekir. Montaj sonrasında, temas ettirilen boruların işlenmiş uçları arasında, çapı 110 mm'ye kadar olan borular için 0,5 mm'yi, 110 mm'nin üzerindeki çaplar için ise 0,7 mm'yi aşan boşluklar olmamalıdır. Kaynak için hazırlanan boruların bağlı uçlarının dış çevre boyunca yer değiştirmesi, boru et kalınlığının% 10'unu geçmemelidir.
Kaynak işlemi sırasında kontrol, kaynak modu ve çevriminin temel parametrelerinin sıkı bir şekilde gözlemlenmesi amacıyla gerçekleştirilir. Doğrudan ısıtmalı boruların alın kaynağının ana parametrelerinin yaklaşık değerleri tabloda verilmiştir. 4.2.
Prosesin ana parametresi, ±10 K hassasiyetle sabit tutulması gereken kaynak aletinin ısıtma sıcaklığıdır. Isıtma süresi - kaynak yapılan boruların uçlarının bir kaynak aletiyle eritilmesi - ortam sıcaklığına bağlıdır , boru duvarının kalınlığı ve boru uçlarının kaynağa hazırlanması. Sabit bir alet sıcaklığında ısıtma süresinin azaltılması, malzemenin yetersiz yumuşamasına ve bunun sonucunda kaynak kalitesinin bozulmasına yol açar. Isıtma süresine tam olarak uymak her zaman sabit bir ısıtma derinliğini garanti etmez; çevre koşullarına bağlı olarak değişiklik gösterebilir.
Kaynak aleti ısıtıldığında tüm çevre boyunca boruların kenarlarına temas etmelidir. İşlem doğru şekilde gerçekleştirilirse, borunun tüm çevresi boyunca yüksekliği 2-3 mm'yi geçmeyen bir rulo şeklinde tek tip bir erimiş malzeme damlası oluşmalıdır.
Boruların uçlarını erittikten sonra hızlı bir şekilde ısıtıcıyı çıkarıp boruları oturtmak gerekir. Isıtıcının çıkarılması ile boruların yerleştirilmesi arasındaki süre 1-2 saniyeyi geçmemelidir, aksi takdirde kaynak yapılacak yüzeylerin hızlı soğuması sonucu kaynağın mukavemeti azalacaktır. Basınç arttıkça eriyen malzeme aşırı derecede sıkışarak borunun içine girer ve bu da kaynaklı bağlantının kalitesini bozar. Basınç altında soğuma süresi, kaynak yapılan boruların et kalınlığı, ortam sıcaklığı ve plastik türü dikkate alınarak belirlenir. Malzeme tamamen sertleşene kadar kaynaklı bağlantı basınç altında tutulmalıdır, çünkü kaynaktan hemen sonra boru uçlarının hareketi bağlantı yerinde ek iç gerilimlerin oluşmasına yol açabilir.
Tablo 4.2. Isıtılmış bir aletle boruların alın kaynağı modunun parametrelerinin yaklaşık değerleri
Seçenekler | Boru malzemesi | |||
---|---|---|---|---|
AYPE | HDPE | PP | PVC | |
Kaynak sıcaklığı (araç), K |
493±10 | 473±10 | 473±10 | 482±5 |
Borunun ısıtılması sırasındaki sıkıştırma basıncı, MPa | 0,02-0,05 | 0.02-0,05 | 0.04-0,08 | 0,05-0,08 |
Boru et kalınlığı (mm) ile birlikte ısıtma süresi (s)**: 4 6 8 10 12 14 16 | 35 50 70 85 100 120 160 | 50 70 90 110 130 160 180 | 60 80 90 100 150 180 230 | 35 45 50 60 70 - - |
Üzücü basınç, MPa | 0,1-0,2 | 0,2-0,3 | 0,2-0,3 | 0.2-0,3 |
Boru et kalınlığı (mm) ile bağlantı yerinin basınç altında soğutulması için gereken süre (dk): 4-6 7-12 14-16 | 3-4 5-8 10-15 | 3-5 6-9 10-15 | 3-5 6-10 12-16 | 2-3 3-5 - |
* NP ve HDPE - sırasıyla düşük ve yüksek yoğunluklu polietilen; PP - polipropilen; PVC - polivinil klorür.
** ortam sıcaklığında 293 K.
Kaynak sonrası kaynak aleti üzerinde kalan erimiş malzeme kazıyıcı, metal fırça ve bez kullanılarak temizlenmelidir.
Kaynak işlemine doğru bağlılık şu şekilde belirlenebilir: dış görünüş ve kaynaklı bağlantının şekli. Kaynaklı bağlantının en yüksek kalitesi, kaynağın tüm çevresi boyunca eşit kalınlıkta çift, düzgün yuvarlatılmış bir kordonun oluşmasına karşılık gelir.
HDPE boru kaynak teknolojisi
Merkezleyici, iki sıkıştırma kelepçesinden oluşan bir yapıdır - sabit olan, doğrudan kılavuzlara sabitlenmiş ve hareketli olan, onunla birlikte monte edilmiştir. Hareketli taşıyıcı, bir pompa tarafından tahrik edilen iki hidrolik silindir kullanılarak iki kılavuz boyunca hareket etme kabiliyetine sahip olacak şekilde monte edilmiştir. . Taşıyıcılar, kaynak yapılacak boruları menteşeli vidalar yardımıyla sıkıştırabilen sabit alt ve üst çıkarılabilir yarım kelepçeler şeklinde yapılmıştır. Çeşitli çaplardaki boruların kaynaklanması için makine, merkezleyicinin yarım kelepçelerine vidalarla sabitlenen değiştirilebilir gömleklerle donatılmıştır.
Düzeltici, üzerine bir bıçağın takıldığı birbirine bağlı iki diskten oluşur. Mandallı bir tutamak sayesinde diskler burçların içinde dönebilmektedir. Düzeltici, çalışma sırasında düzelticinin merkezleyici kılavuzlara monte edildiği iki destekle donatılmıştır.
Ön panel, üzerine şekillendirilmiş ürünlerin montajı için tasarlanmıştır (flanşlar için burçlar ve D63'ten 225 mm'ye kadar geçişler); ikincisini sabitlemek için ön panele kelepçeler monte edilmiştir. Ön plaka hareketli taşıyıcıya takılıp sıkıştırılırken, adaptörleri ve burçları flanşın altında ortalamak ve kelepçelemek için kullanılırlar.
Makinenin çalışma prensibi kaynak yapılacak boruları ortalayıp sabitlemek, kaynak yapılacak boruların uçlarını kaynağa hazırlamak ve daha sonra ek yerinin uçlarını ısıtmaktır. Boru uçlarının hazırlanması, bunların kir, toz ve diğer maddelerden temizlenmesini ve ardından bağlı yüzeylerin bir düzeltici kullanılarak kesilmesini içerir. Boruların uçları kelepçelerden 55-60 mm'den fazla çıkıntı yapmamalıdır.
Boruların hazırlanan uçları HDPE için 220 C, LDPE için 200 C sıcaklığa kadar ısıtılır. Isıtma, kaynak yapılan boruların uçları arasına monte edilen bir ısıtıcı ile gerçekleştirilir. Boruların uçları hidrolik bir tahrik kullanılarak manüel olarak ısıtıcıya (yeniden akışın 1. aşaması) getirilir, 0,49 X 10... 0,78 X 10 Pa (0,5...0,8 kgf/cm) basınç oluşturulur ve böylece boruların uçlarının ısıtıcının düzlemlerine sıkı bir şekilde oturması (aşama II yeniden akış). Gerekli basınç Pompaya monte edilmiş bir basınç göstergesi tarafından kontrol edilir.
Belirtilen ısıtma süresinden sonra boruların uçları ısıtıcıdan çıkarılır, ısıtıcı çıkarılır ve boruların uçları 2,00 X 10 + 0,04 X 10 Pa (2,0 + 0,04 kgf) basınç artışıyla birbirine bastırılır. HDPE borular için /cm) ve LDPE borular için 0,98 X 10 + 0,025 X 10 Pa (1,0 + 0,025 kgf/cm).
- Gerekli sıkıştırma basıncı Tablo 3'e göre seçilir. Boru dizilerinin uçlarını bir araya getirmek için gereken çekme kuvveti referans değerine eklenir.
- Kaynak, hareketli taşıyıcının ters hareketi sırasında gerçekleştirilir (Ayırma). Kaynak parametreleri tabloda verilmiştir.
Birleştirmek
Çalışma prensibi
Daha sonra kaynak dikişi basınç altında soğutulur. Polietilen boruların kaynak işlemi aşamalarının süresi Tablo 3'e uygun olmalıdır. Isıtma sırasında 2. erime aşamasının erime süresi, ortam sıcaklığına (t ortam) bağlı olarak bir artışa göre ayarlanmalıdır. 10 saniyeye dayalıdır. sıcaklık düştüğünde 1 derece artar (normal çalışma sıcaklığı 20° C).
HDPE boruların parametresi, mm | Boru uçlarının erimesi | Teknolojik mola C, artık yok | Kaynak | ||||||||||
---|---|---|---|---|---|---|---|---|---|---|---|---|---|
Çap | duvar kalınlığı | İlk aşama | İkinci aşama | Rahatsız edici basınç artış süresi, C, artık yok | Yerleşme basıncı, Çiğ, kgf/cm2 | ||||||||
Basınç, Popl, Kg/cm2 | Süre C, artık yok | Çapak yüksekliği, mm | Basınç, kgf/cm2 | Pro- mutlak- güçC, artık yok | Çapak yüksekliği, mm | Taşıyıcının sıkıştırma hareketi | Taşıma seyahati | Basınç soğutma süresi dk | |||||
Taşıyıcının sıkıştırma hareketi | Taşıma seyahati | ||||||||||||
63 | 2,0 | 0,9 (+0,1) | 15 | 0,5 | 0,2...0,5 | 40 (+10) | 2 (+1) | 3 | 4 | 1,2 (+0,1) | 8 (+2) | ||
2,5 | 1,1 (+0,1) | 45 (+10) | 1,4 (+0,1) | ||||||||||
3,6 (+0,6) | 1,4 (+0,1) | 50 (+10) | 1,9 (+0,1) | ||||||||||
5,8 (+0,6) | 2,1 (+0,1) | 55 (+10) | 2,8 (+0,1) | ||||||||||
110 | 2,7 (+0,5) | 2,0 (+0,1) | 40 (+10) | 3,0 (+0,1) | |||||||||
4,3 (+0,7) | 3,0 (+0,1) | 50 (+10) | 4,0 (+0,1) | ||||||||||
6,3 (+0,9) | 4,3 (+0,1) | 65 (+10) | 3 (+1) | 4 | 5,7 (+0,1) | ||||||||
10,0 (+1,2) | 8,0 (+0,2) | 25 | 85 (+15) | 6 | 10,7 (+0,1) | 12 (+3) | |||||||
160 | 3,9 (+0,6) | 4,4 (+0,2) | 15 | 45 (+10) | 2 (+1) | 3 | 4 | 5,9 (+0,2) | 8 (+2) | ||||
6,2 (+0,9) | 6,5 (+0,2) | 60 (+15) | 4 | 8,5 (+0,2) | |||||||||
9,1 (+1,2) | 8,9 (+0,2) | 25 | 85 (+15) | 3 (+1) | 11,8 (+0,2) | 12 (+3) | |||||||
14,6 (+1,7) | 13,0 (+0,2) | 35 | 0,8 | 130 (+15) | 5 | 6 | 17,5 (+0,3) | 15 (+3) | |||||
225 | 5,5 (+0,8) | 8,6 (+0,1) | 15 | 0,5 | 55 (+15) | 2 (+1) | 4 | 4 | 11,5 (+0,3) | 8 (+2) | |||
8,7 (+1,1) | 12,5 (+0,2) | 25 | 80 (+15) | 3 (+1) | 6 | 16,7 (+0,3) | 10 (+3) | ||||||
12,8 (+1,5) | 17,4 (+0,2) | 35 | 0,8 | 120 (+15) | 5 | 7 | 23,0 (+0,3) | 15 (+3) | |||||
20,5 (+2,3) | 25,0 (+0,2) | 50 | 1,0 | 180 (+20) | 4 (+1) | 6 | 10 | 34,5 (+0,3) | 25 (+5) |
HDPE boruların alın kaynağı. Alın kaynak teknolojisi.
Alın kaynağının temel hükümleri
Kaynak yapılacak elemanların kimyasal ve fiziksel olarak uyumlu olması ve bu uyumluluğun boru ve bağlantı parçaları üreticisi tarafından belgelendirilmesi gerekir. Borular aynı et kalınlığına ve aynı çapa sahip olmalıdır.
Kaynak aşağıdaki koşullara bağlı olarak gerçekleştirilir:
- Düşük sıcaklık, rüzgar, toz ve kirlilik koşullarında, kaynak işleri için korunaklı bir alan oluşturmak amacıyla (düşük sıcaklıklarda ısıtılan) bir çadır kullanılması gerekir. Alınan önlemlerin yeterli olduğundan emin olmak için kaynaklı birleşimler üzerinde testler yapılmalıdır.
- Boruların uçları kaynak aşamasına kadar temiz kalmalıdır.
- Kaynak sırasında boruların uçları aynı sıcaklığa kadar ısıtılmalıdır (güneş ışığından korunmalıdır).
- Kaynak sırasında (ve özellikle soğutma aşamasında) her türlü mekanik darbeden kaçının.
- Boruların kaynak işlemine dahil olmayan uçları hava akımından soğumaması için tapalarla kapatılmalıdır.
- Borunun hareketini kolaylaştırmak ve sürtünmeyi azaltmak için yerleştirme silindiri kullanılması tavsiye edilir.
Genel Hükümler
Kaynak prensibi şu şekildedir: Kaynak yapılacak yüzeyler bir termoelemente (belirli bir basınçta, belirli bir süre) bastırılır. Çapak standartların belirlediği yüksekliğe ulaştığında termoelement çıkarılır ve kaynak yapılacak parçalar (bir süre basınç altında) birleştirilir.
Alın kaynağının prensibi ve çeşitli aşamaları.
Kaynak döngüsünün 5 aşaması vardır:
- Erime aşaması (çapak oluşumu)
- Isıtma aşaması
- Termal eleman (ayna) çıkarma aşaması
- Kaynak aşaması
- Soğutma aşaması
Süre ve baskı düzenlemelere bağlı olarak değişir. Aşağıda kaynak döngüsünün ana aşamaları ve amaçları yer almaktadır.
Yeniden akış aşaması
Bu aşamada çapak oluşumu süreci meydana gelir. Kaynak yapılacak elemanların hazırlanmasını takip eder (konumlandırma, kaplama, parametrelerin hesaplanması, kaynak için gerekli sıcaklığa ısıtma) ve işlem sırasında kalan küçük parçacıkların giderilmesine olanak tanır.
PE boruların ısıtma aşaması
Bu aşamada sıcaklık malzemeye yayılır ve derin bir ısınma meydana gelir. Temel olarak, basınç sıfıra yakındır (kaynaklı yüzeylerin birbirinden uzak olmaması için yalnızca harekete karşı direnç kuvvetini telafi etmelidir) Isıtma elemanı).
Kaynaştırıcı çıkarma aşaması
Bu aşamada ayna çıkartılarak kaynak yüzeyleri bağlanır. Sıcaklık kaybını önlemek ve kaynaklı bağlantının kalitesini etkileyebilecek yabancı parçacıkların (toz, kum...) riskini azaltmak için bu aşama mümkün olduğu kadar kısa olmalıdır.
PE boru kaynak aşaması
Bu aşamada bağlantının homojenliği sağlanarak son çapak ve moleküler bağlar oluşturulur.
PE boruların soğutma aşaması
Kaynak tamamlandıktan sonra bu adım, bağlantının gücünü tehlikeye atabilecek stres veya şoku önler.
Alın kaynağı için çeşitli standartlar.
Zaman ve baskı, kullanılan normatif belgelere bağlıdır. Aşağıda kaynak döngüsünün aşamaları ve bunların her biri için süreler ve basınçlar verilmiştir.
e - duvar kalınlığı, Dn - nominal çap, S - kaynak yüzeyi, fct (: bağlı olarak)
Sıcaklık ısıtılır. eleman | P1 | t1 | P2 | t2 | t3 | P4 | t4 | P5 | t5 | |
---|---|---|---|---|---|---|---|---|---|---|
DVS 2207 1995 e< 70mm | 200 C - 220 C | 0,15MPa | 0,5- 4 mm |
0 MPa | 10e | Fct(e) | 0,15MPa | Fct(e) | ||
DVS 2207 1995 e<50mm | 195C-220C | 0,15MPa | 0,5 - 3,5 mm |
0 MPa | 190 -xxx | Fct(e) | 0,15MPa | Fct(e) | ||
WRCWIS e>20mm | 230°C+-10 | 0,15MPa | Grat = 2 mm |
0 MPa | 10e | 0,15MPa | 10'lar | 0,15MPa | 50 e | |
DS/INF | 200 C - 220 C | 0,18MPa | Grat = 0,5 + 0.1e |
0,01MPa | 15e | 3+ 0,01Dn | 0,18MPa | 3 + 0,03Dn | 0,18MPa | 10s + 0,5e |
VEG 85 NEN 7200 | 210°C+-10 | 0,18MPa | Grat = 0,5 + 0.1e |
0 MPa | 12e | 3+ 0,01Dn | 0,18MPa | 3 + 0,03Dn | 0,18MPa | 10s + 0,5e |
Electrabel Becetel I 110-250mm | 210°C+-10 | 0,05 MPa | 10e | < 3s | 0,3 MPa | Fct(S) | ||||
Electrabel Becetel I 250-315 | 210°C+-10 | 0,05 MPa | 10e | < 3s | 0,24MPa | 10'lar | 0,05 MPa | Fct(S) | ||
GASTEC | 220°C+-15 | 0,18MPa | Grat = 0,5 + 0.1e |
0,01MPa | 12e | 4 + 0,01 e | 0,18 Mpa (4+0,03e) | 3+e dk | 0,01MPa | 1,5e dk. |
GAZ Doğal Si Dn=315 | 225°C+-15 | 0,18MPa | 1-2mm veya 2-3 mm DN 160 ise |
0,03 00,2 MPa | Dn/2 + 30 +- 10 | 4. gün< 200 5 >250 6 |
0,18MPa | >10 dakika | 1,5e dk c maksimum 20 dk |
UNI STANDARTLARI:
- e: Boru kalınlığı
- Dn: Nominal çap
- b: çapak yüksekliği = 0,5 + (0,1e) mm
- t1: çapak süresi = fct (b) = 0,5 + (0,1e) mm
- t2: ısıtma süresi = 12e
- t3: maksimum ayna çıkarma süresi = 4 + (0,3e) sn
- t4: maksimum basınç yükselme süresi = 4 + (0,4e) sn
- t5: kaynak süresi = (3 + e) min
- t6: soğuma süresi = (1,5e) dk
Duvarları 20 mm veya daha büyük olan boru ve bağlantı parçalarının kaynaklanması için faz 6 eklenir, diğer durumlarda faz 5'e dahil edilir.
S = mm2 cinsinden kaynak alanı = Pi(Dn2 - Di2)/4
Sc = mm2 cinsinden makine silindir alanı
- e: Boru kalınlığı
- Dn: Nominal çap
- Di: İç çap (Dn-2e)
- Sc: mm2 cinsinden makine silindir alanı (4,32 cm2, 5,88 cm2, 8,46 cm2)
- b: dikiş yüksekliği = 0,5 + (0,1e) mm
- T: Isıtma elemanı sıcaklığı
- P1: Parlama basıncı = 0,15 (S/Sc) x 10 (bar)
- P2: Isıtma basıncı = 0,02 (S/Sc) x 10 (bar)
- P5: Kaynak Basıncı = 0,15 (S/Sc) x 10 (bar)
- P6: Soğutma basıncı = e 20 mm 0 ise
- e 20 mm ise 0,05 (S/Sc) x 10 (bar)
- t1: çapak oluşum süresi = fct (b) = 0,5 + (0,1e) mm
- t2: ısıtma süresi = (10t) + 60 sn
- t3: maksimum ayna çıkarma süresi = 10 sn
- t4: 10 saniye
- t5 : kaynak süresi = e 20 mm ise (3 + e) min
- e 20 mm ise 10 sn
- t6: soğuma süresi = e 20 mm = 0 ise
- e 20 mm= (3 + e) min ise
Hesaplama için aşağıdaki değerleri alıyoruz:
S = mm2 cinsinden kaynak alanı = Pi(Dn2 - Di2)/4
Sc = mm2 cinsinden makine silindir alanı
- e: Boru kalınlığı
- Dn: Nominal çap
- Di: İç çap (Dn-2e)
- Sc: mm2 cinsinden makine silindir alanı (4,32 cm2, 5,88 cm2, 8,46 cm2)
- b: çapak yüksekliği= 0,5 + (0,1e) mm
- T: Isıtma elemanı sıcaklığı: Tabloya bakın
- P1: Yeniden akış basıncı = 0,15 (S/Sc) x 10 (bar)
- P2: Isıtma basıncı = 0,02 (S/Sc) x 10 (bar)
- P5: Basınçlı Kaynak-Soğutma = 0,15 (S/Sc) x 10 (bar)
- t1: yeniden akış süresi = Tabloya bakın
- t2: ısıtma süresi = Tabloya bakın
- t3: maksimum ayna çıkarma süresi = Tabloya bakın
- t4: maksimum sıkıştırma süresi = Tabloya bakın
- t5: kaynak süresi = Tabloya bakın
Elektrofüzyon veya elektrofüzyon kaynağı
Elektrofüzyon kaynak makineleri polietilen ve polipropilen boruların birleştirilmesinde kullanılır. Elektrofüzyon cihazlarının çalışma prensibi, kaynak yapılacak boruların, bağlanacak borunun dökme malzemesi ve bir ısıtma elemanından oluşan özel bir kaplinin içine yerleştirilmesidir. Isıtma elemanının (genellikle yüksek dirençli bir tel) ısıtılması sırasında, plastik kütlenin bir kısmı erir ve kaynaklı bir bağlantı oluşturmak üzere borunun toplam kütlesi ile birleşir.
Elektrofüzyon kaplininin kaynak sonrasında boru üzerinde kalması nedeniyle, bu tür bir bağlantı pahalı ve kalitelidir, bu da gaz borularının kaynaklanması sırasında önemlidir. Bu yöntem, basınç altında gaz boru hatlarına kaynak yapılmasına ve delinmesine ve ayrıca plastik boru hatlarının onarılmasına olanak tanır. Ek olarak, elektrofüzyon kaynak makineleri herhangi bir alın kaynak makinesine kıyasla nispeten hafiftir ve neredeyse her çaptaki boruları bağlamanıza olanak tanır.
Elektrofüzyon cihazları aşağıdaki tiplere ayrılır:
- basınçsız boru hatlarını kaynaklamak için elektrofüzyon makineleri (kapsamı sınırlı olmasına rağmen çok hafif);
- kaynak döngüsünü kaydetmeden basınçlı boru hatlarının kaynaklanması için elektrofüzyon makineleri;
- Kaynak döngüsünün kaydedildiği basınçlı boru hatlarının kaynaklanması için elektrofüzyon makineleri.
Plastik boru hatları, özellikleri bakımından çelik ve bakır borulardan üstün oldukları için metal boru hatlarını günlük hayatımızdan çıkarmaktadır: kurulum ve bakım kolaylığı, agresif ortamlara dayanıklılık ve düşük düzeyde yerel direnç. Ancak bu görünen basitliktir. Plastik boru hatları gerektirir yüksek seviye boru tesisatı kültürü ve yeterli düzeyde bilgi - boruların ne zaman, hangi koşullar altında ve ne şekilde monte edilebileceği. Bu nedenle birçok alet ve boru üreticisi, boru hattı kurulumuyla ilgili ücretsiz seminerler ve çalıştaylar düzenlemekte ve ayrıca kurulumcuların becerilerini geliştirmek için özel eğitim programları da sunmaktadır.
Çeşitli plastik iletişimlerin gücü ve dayanıklılığı, polipropilen boruların lehimleme sıcaklığının ne kadar doğru dikkate alındığına bağlıdır. Polipropilen ürünleri kaynak yaparken malzemenin ısınma süresini ve bağlantı yerlerinin soğuma süresini hesaba katmak gerekir. Polipropilenden üretilen teknik ürünlerin lehimleme işleminin sıcaklık ve zaman parametrelerinin doğru karşılaştırılması ve dikkate alınması, dayanıklı ve güvenilir bir malzemenin üretilmesine katkıda bulunur. Teknolojiden saparsanız ürün birleşim yerlerinde kopmalar olur ve kalitesiz olur.
Genel bilgi
Polipropilen boru ürünlerini lehimlemek için sıcaklık rejimi doğrudan kullanılan polimere bağlıdır. Uygulamada 4 tip malzeme kullanılmaktadır:
- +40 0 C'ye kadar sıcaklıklarda teknik ürünlerin kullanımında kullanılan PN10;
- +60 0 C'de kullanım için PN16;
- PN20, +80 0 C ile +95 0 C arası su temininde kullanılır;
- +95 0 C üzerindeki çalışma modları için PN25.
Sıcaklık rejimini korumanın yanı sıra, belirli bir işarete sahip boru teknik ürünlerinin dayanabileceği basınca da bağlıdır.
İlk tip, soğuk su temini amaçlı teknik ürünlerin döşenmesinde kullanılır. PN20 işaretli boru ürünleri evrensel olarak kabul edilir ve soğuk ve sıcak su temini için tasarlanmıştır, ancak +95 0 C'nin etkisinin kısa vadeli olduğu dikkate alınır. Sıcaklık korunmazsa, etkisi nedeniyle sıkılığını kaybedecek ve deforme olacaktır.
Lehimleme modu ve süreç üzerindeki etkisi
Onları ısıtmaktan oluşur, ardından içerdikleri plastik yumuşar. İki ısıtılmış ürün bağlandığında, bir teknik ürünün polipropilen moleküllerinin diğerinin moleküllerine difüzyonu (birbirine nüfuz etmesi) meydana gelir. Sonuç olarak, ortaya çıkan malzemeyi hava geçirmez ve dayanıklı hale getiren güçlü bir moleküler bağ oluşur.
Yetersiz mod varsa, iki malzeme birleştirildiğinde yeterli difüzyon meydana gelmeyecektir. Sonuç olarak, teknik ürünün birleşim yeri zayıf olacak ve bu da tüm malzemenin sıkılığının ihlal edilmesine yol açacaktır.
"Not!
Fitting ve boru teknik ürününün kaynak sırasında aşırı ısınması parçaların deformasyonuna neden olur. Geometrileri bozuldu ve iç kısımda silindir akışı var.”
Çıkış, kavşakta çapı teknolojik standartları karşılamayan minimum iç deliğe sahip bir boru hattıdır.
Polipropilen boruların kaynağında sadece ısıtma sıcaklığının değil, aynı zamanda zamanın, ortamın sıcaklık koşullarının ve teknik ürünlerin çapının da dikkate alınması gerekir. Boru malzemelerinin ısınma süresi doğrudan çaplarına bağlıdır.
Dış ortam önemlidir. Polipropilen ürünleri kaynaklarken izin verilen minimum sıcaklık -10 0 C'dir. İzin verilen maksimum sıcaklık +90 0 C'dir. Polipropilen boruların kaynaklanması için sıcaklık tablosu, her şeyin temelde zamana bağlı olduğunu açıkça göstermektedir.
Dış ortamın lehimleme kalitesi üzerinde güçlü bir etkisi vardır. Bunun nedeni, malzemelerin kaynak makinesinden çıkarıldığı andan doğrudan bağlanana kadar zamanın geçmesidir. Böyle bir duraklama kaynağın kalitesini büyük ölçüde etkiler. Atölyedeki dış sıcaklık düşükse, birleştirilen ürünlerin ısınma süresinin birkaç saniye artırılması tavsiye edilir. 20 mm polipropilen boruların dış lehim sıcaklığı 0 0 C'nin üzerinde olmalıdır. Aşırı ısınmaması önemlidir. Boru malzemesinin iç deliğine polimerin akması ve iç lümenini azaltma riski vardır. Bu, boru hattının gelecekteki bölümünün verimini büyük ölçüde etkileyecektir.
Sıcaklık kontrolü, özellikleri
Polipropilen boruların kaynağı için hangi sıcaklığın gerekli olduğuna cevap vermeden önce, kullanılan kaynak makinesine karar vermelisiniz. Polipropilenden yapılan malzemeleri lehimlemek için bir havya kullanılır. Şu soru ortaya çıkıyor: Polipropilen boruları lehimlemek için havya hangi sıcaklığa ayarlanmalıdır? Optimum değer 260 0 C'dir. 255 0 -280 0 C aralığında kaynak yapılmasına izin verilir. Havyayı 271 0 C'nin üzerinde aşırı ısıtırsanız, ısıtma süresini kısaltırsanız, ürünlerin üst katmanı dahili olandan daha fazla ısınır. Sızdırmazlık filmi çok ince olacaktır.
Polipropilen boruların lehimlenmesi için bir sıcaklık tablosu vardır.
Kaynak süresi | Isıtma süresi, s | Soğutma süresi, s | |
4 | 6 | 120 | 259-280 |
25 | 4 | 7 | 180 |
4 | 8 | 240 | 259-280 |
40 | 5 | 12 | 240 |
5 | 18 | 300 | 259-280 |
63 | 6 | 24 | 360 |
6 | 30 | 390 |
20 mm polipropilen boruların kaynak sıcaklığı 259 ila 280 0 C arasında değişirken, 25 mm polipropilen boruların kaynak sıcaklığı da değişmektedir.
Cam elyaf takviyeli polipropilen boruların kaynak sıcaklığı gibi bir gösterge için özel bir gereklilik yoktur. Polipropilenden yapılmış diğer teknik ürünlerle aynı aralıkta yer almaktadır. Kaynak yapmadan önce bu tür ürünlerden üst güçlendirilmiş tabakanın tıraş makinesi ile çıkarılması gerekir.
Polipropilen ürünleri kaynaklarken aşağıdaki özellikler vardır:
- ısı kaybı meydana geldiğinden ve kaynak sıcaklığının düşmesinden dolayı dikişin kalitesinin düşmesine neden olduğundan havya ile kaynak alanı arasında büyük mesafelerden kaçınma ihtiyacı;
- boru hattının deformasyonunun ve bölümlerinde statik stres oluşmasının bir sonucu olan iki ürün arasına bir havya monte edilememesi nedeniyle ustanın son bağlantıyı yapmadığı lehimleme prosedürünün ihlali;
- yapısal parçaların sıralı ısıtılmasının kabul edilemezliği.
Bağlantı parçası ve boru malzemesi sırayla değil, aynı anda ısıtılmalıdır. Parçaların eşit şekilde ısıtılması gerekliliğine uyulmaması, tüm proses teknolojisinin bozulmasına neden olacaktır.
Nihayet
Sürecin etkinliğini sağlamak için sıcaklık rejiminin teknolojik gereksinimlere uygun olarak ayarlanması, kaynak için yüksek kaliteli bir ünite kullanılması, kaynak alanı ile kaynak alanı arasındaki mesafenin 1,4 m olması ve odanın yeterli olması gerekir. ısıtılmış.
Manuel makineler en basitleridir, esas olarak alın kaynağı için tasarlanmıştır polietilen borular küçük çaplı. Manuel makinelerde tüm kaynak parametreleri doğrudan kaynakçılar tarafından aşağıdaki kurallara göre ayarlanır: kaynak masaları ve iki boruyu bağlama işlemi manuel olarak yapılır.
Yarı otomatik cihazlarda zaten iki boruyu manuel olarak değil, bir hidrolik istasyon ve bir hidrolik merkezleyici kullanarak bağlamanıza olanak tanıyan bir hidrolik sistem bulunmaktadır, bu da kaynakçının işini çok daha kolaylaştırır. Bu tür makineler, manuel kaynağın aksine esas olarak daha büyük çaplı polietilen boruların kaynaklanması için kullanılır. Ancak yarı otomatik cihazlarda kaynak modları ayrıca doğrudan kaynakçı tarafından manuel olarak ayarlanır.
Kaynak parametrelerinin manuel olarak ayarlanması, kaynaklı bağlantının kalitesini etkileyen hatalara yol açabilir. İnsan faktörünün etkisini ortadan kaldırmak için kaynak işleminin bilgisayar kontrollü otomatik alın kaynak makineleri (CNC makineleri, SUVI) icat edildi. Kaynakçı polietilen borunun çapını, SDR'sini ve malzemesini girdikten sonra kaynak modları otomatik olarak ayarlanır. Daha sonra otomatik makine insan müdahalesine gerek kalmadan kaynağı kendisi gerçekleştirir.
Kaynak tablolarına göre kaynak modlarına uygunluk, yüksek kaliteli bir son bağlantıya yol açar. Kaynak tabloları aşağıdaki parametreleri gösterir:
Duvar kalınlığı;
. kaynak basıncı (sıfır basınca eklenen basınç);
. ilk çapak genişliği;
. boru ön ısıtma aşamasındaki basınç;
. boru uçlarının ısınma süresi;
. geçiş süresi (ısıtma elemanının çıkarılma süresi);
. boru yerleştirme aşamasında basınç oluşturma zamanı;
. Çalışma basıncı altında bağlantının soğuma süresi.
Tabloda yer almayan bir diğer parametre ise cihazın ısıtma elemanının sıcaklığıdır. Bu parametre bir borunun alın kaynağı için daha az önemli değildir. Doğru sıcaklık ayarı şunlara bağlıdır: malzeme polietilen borunun yapıldığı yer. Aşağıda ısıtma elemanının sıcaklığını ayarlamak için grafikler bulunmaktadır.
Aşağıda kaynak modlarının bir özet tablosu bulunmaktadır.
Nominal duvar kalınlığı, mm |
Çapak oluşumu, mm (minimum değerler) |
Donaheat, sn. |
Isıtma elemanının çıkarılması, sn (maksimum süre) |
Yerleştirme, sn. |
Soğutma, dk. |